Best Practices for Purchase Managers to Manage Packaging Inventory
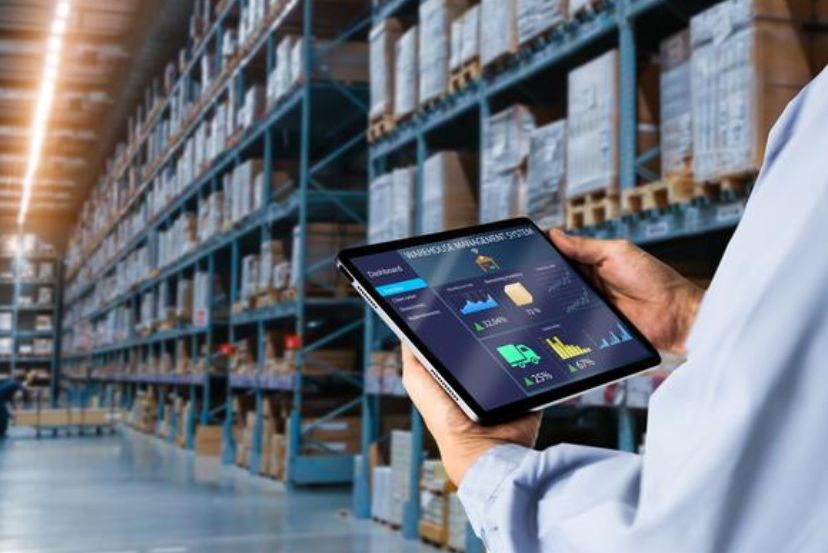
Efficient packaging inventory management is crucial for purchase managers to enhance operational efficiency and boost profitability.
By ensuring timely deliveries and controlling costs, effective inventory practices directly impact business success.
However, if you don’t have strategies in place, managing packaging materials can be difficult!
In this blog, we’ve put together the best tips and practices to help you simplify your processes and ensure your packaging inventory management is running smoothly.
So, without any further ado, let’s begin. But first, let’s understand packaging inventory management in detail.
Understanding Packaging Inventory Management
Packaging inventory refers to the materials used to wrap and protect products during transportation to customers or retail locations.
It includes items such as caps, lids, boxes, fillers, jars, cans, and other materials essential for ensuring products reach their destination intact.
To effectively manage packaging inventory, it’s essential to keep and monitor warehouse materials to guarantee that the required packaging supplies are on hand for production and shipment timelines.
A well-implemented packaging inventory system streamlines packing and shipping, ensuring smooth operations and timely deliveries.
Conversely, an unmanaged system can lead to delays, increased costs, and disruptions in workflow.
Understanding the fundamentals of inventory management in packaging can help procurement managers streamline supply chain operations efficiently and cost-effectively while improving customer satisfaction.
Why is Packaging Inventory Management Important?
Proper packaging inventory management is essential for several reasons:
- Smooth Operations: Guarantee that packaging supplies are consistently accessible as required to avoid any interruptions in manufacturing or delivery processes.
- Optimizing Costs: Minimizing expenses related to inventory storage and material waste.
- Customer Satisfaction: Proper packaging ensures customers receive undamaged products. This enhances customer satisfaction.
For purchase managers, managing packaging inventory effectively means striking the perfect balance between demand and supply to achieve operational excellence.
What Are the Challenges in Packaging Inventory Management?
Managing packaging inventory can be tricky, demanding time and effort and requiring a solid understanding of product flow and materials.
Here are common challenges and how effective management can help tackle them:
Space Limitations & High Storage Costs
- Storing packaging materials with products consumes valuable warehouse space, driving up costs.
- Implementing a smart inventory system optimizes storage use and informs decisions about expansion or relocation.
Inconsistent Quality of Materials
- Consistent packaging quality is critical for protecting products and preserving brand image. Variations in material quality can negatively impact customer satisfaction.
- An advanced system ensures uniformity in materials and helps maintain a rigid and consistent brand identity.
Coordination with Product Inventory
- Packaging and product inventory go hand in hand. Poor packaging management can lead to misplaced products or inaccurate stock records.
- A clear process keeps everything on track, reducing shipping costs and improving warehouse organization.
Supply Chain Delays
- Packaging supply chain issues can delay deliveries, impact sales, and frustrate customers.
- Effective management helps predict delays, explore alternative suppliers, and align orders with demand trends to keep operations smooth.
Proper packaging inventory management not only resolves these challenges but also enhances efficiency, reduces costs and improves customer satisfaction.
Benefits of Effective Packaging Inventory Management
Effective packaging inventory management offers several key benefits:
- Cost Savings: Cut expenses by reducing waste and giving accurate insights into ordering and storage.
- Improved Efficiency: Speed up packaging processes and prevent delays, leading to timely delivery of products.
- Quality Control: Increases visibility to monitor material quality closely and catch issues early.
- Sustainability: Use eco-friendly materials and reduce waste to support the environmental impact.
- Better Customer Service: Avoid delays caused by material shortages, ensuring deliveries on time and happier customers.
These benefits highlight why packaging inventory management should be a priority for purchase managers.
How Moglix Helps with End-to-End Packaging Solutions
Moglix offers over 50 packaging categories, delivering to more than 19k pin codes across India.
Our packaging solutions are sustainable, ethically sourced, and globally compliant, encompassing everything from design to delivery.
With large manufacturing capacities for packaging films and products, our packaging services have consistently improved, providing end-to-end solutions for clients throughout India.
Simplify your packaging inventory management with Moglix’s comprehensive solutions. For inquiries, please reach out to us at info@moglixbusiness.com .